Envirogen Group has worked at the Molson Coors Burton-on-Trent site for many years, providing servicing and maintenance for process water treatment across the site. Following a recommendation by its service engineers, Envirogen set out to reduce water and salt usage in the bottle rinsing process.
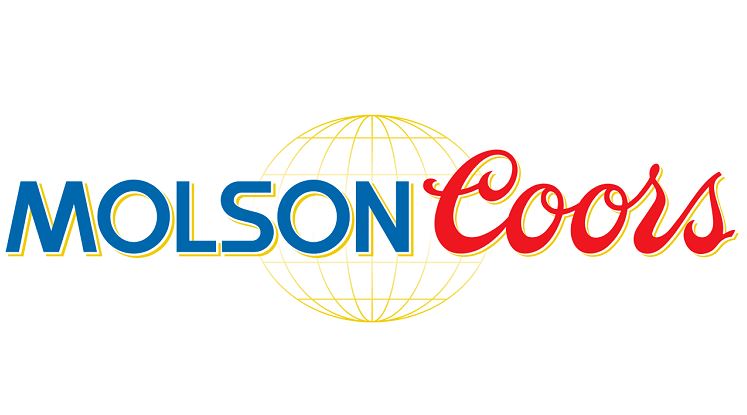
The Molson Coors Burton-on-Trent site is the largest brewery in the UK, producing over 1.2 billion barrels of beer per annum. Although most of the water is used within the brewing process, there is a substantial amount used in auxiliary activities, such as bottle rinsing.
“Molson Coors uses hot water to rinse bottles prior to filling,” explains Bill Denyer, UK and European CEO, Envirogen. “Whenever water is heated, soluble ions, such as calcium and magnesium, can cause scale and leave a residue on bottle surfaces. By using softened water, the calcium and magnesium ions are exchanged with sodium ions that are non-scale forming. The ions stay in solution and no residue is left on the bottles.”
The existing softener on-site was based on traditional co-flow ion exchange technology. The old process water treatment system was dependent on using very high levels of water and salt during its regeneration sequence, something that Molson Coors was keen to address. The brand’s latest Beer Print project aims to reduce water usage in its largest breweries by 22% by 2025. This ambitious target will see a water to beer ratio of 2.8:1 and will be realised, in part, by measures such as the introduction of more efficient water softeners and process water solutions.
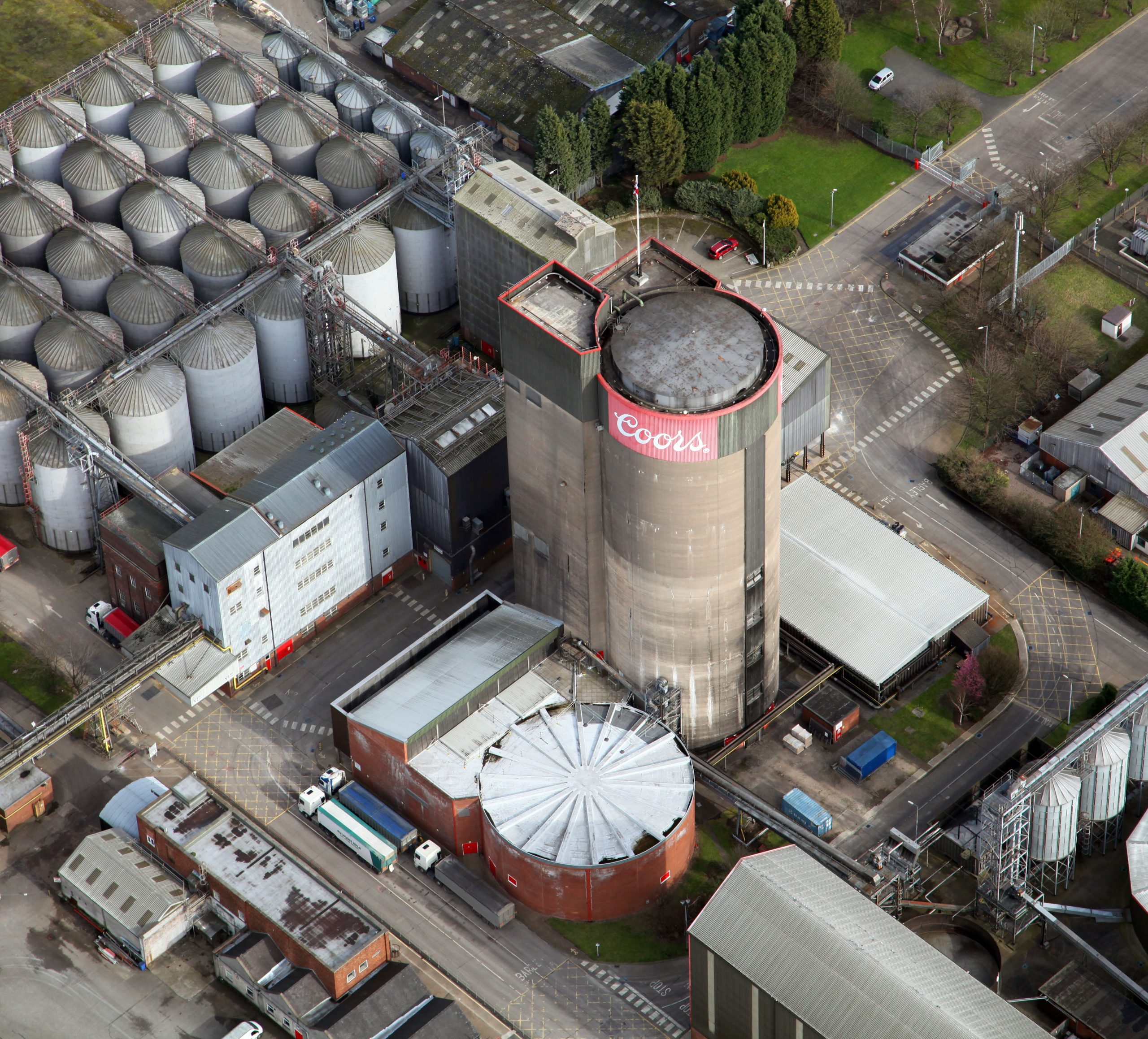
80% reduction in water bills and a 50% reduction in salt deliveries
“The old softener system was sending around 5,000 m³ of rinse water to waste per year and using around 98,000 kg of salt for regeneration. We recommended our EcoSave 1200 duplex co-flow water softener as a way to save up to 80% on rinse water bills and up to 50% on salt usage,” continues Denyer. “This will move Molson Coors closer towards meeting their water efficiency and sustainability targets.
“EcoSave is a counter-current water softener, which means that the resin bed is regenerated in the opposite flow direction to production. When designed correctly, the last 5% to 10% of the resin bed never has contact with hardness salts found in water supplies, thereby providing a higher quality soft water with a more efficient regeneration process, when compared with a co-flow water softener. Highly responsive sensors ensure that regeneration processes stop as soon as the resins are rinsed from any excess brine, which reduces water and salt wastage. Additional sensors measure the water quality as it leaves the system, ensuring a full data trail for quality tracking.
“With the previous system, operators were having to regenerate the water softeners more often to ensure that they were ready for reuse. With EcoSave, and the additional sensors, the system becomes responsive and this drives the large water and salt savings. This translates to a much lower environmental impact and considerable reductions in operational costs, all in a compact, space-saving design. The system will pay for itself within two years and the site will continue to see the financial benefit for many years to come.”
Molson Coors decided to take out an extension to their current Envirogen PureCare service and maintenance plan to include the EcoSave system. The plan ensures that the process water treatment system is kept in prime condition, optimises the overall equipment effectiveness and ensures that Molson Coors continues to save energy and water.
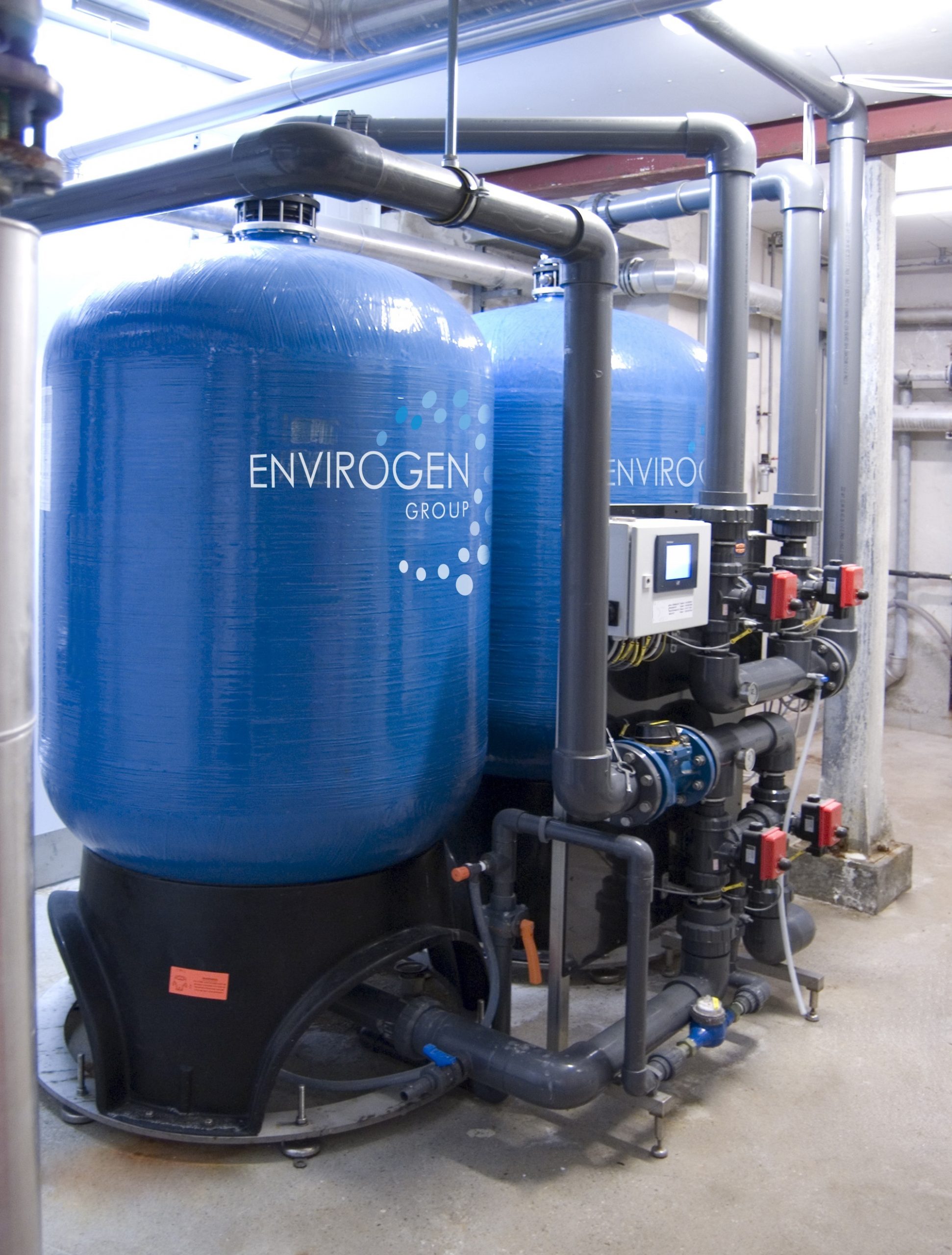
Find information on more Molson Coors projects and other food and beverage case studies.
Key outcomes
• Molson Coors was able to uncover substantial cost savings
• Return on investment achieved within two years
• Rinse water bills reduced by up to 80%
• Salt usage reduced by up to 50%
• The project helped Molson Coors meets its 2020 target of a water to beer ratio of between 3:1 – 3.5:1. It also forms part of the plans to meet the brand’s Beer Print 2025 target to reduce water usage by 22% and achieve a water to beer ratio of 2.8:1.
For a free assessment to evaluate water treatment and process filtration solutions for your site, contact our team of expert engineers
About the client
Molson Coors is a global brewer of beers and ciders with a strong history spanning over 240 years. They own Britain’s biggest brewery at the Burton-on-Trent site where they manufacture well-known beer brands such as Carling, Coors and Miller.
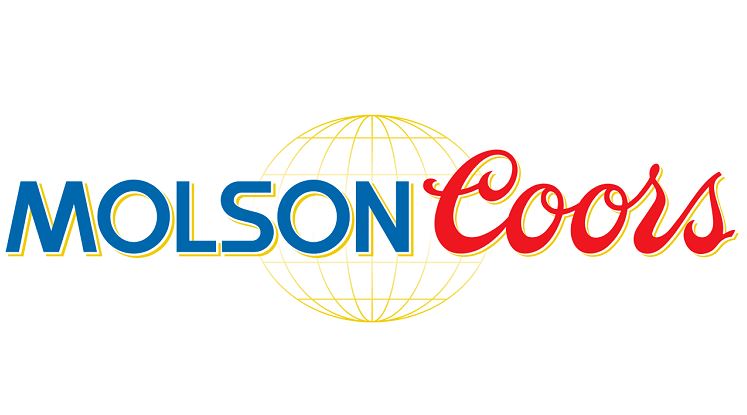