When a mixed bed ion exchange system started to become a bottleneck for operations, our client grew concerned. The ion exchange regeneration process was required more frequently and the flushing cycles were taking longer, draining the buffer tank and causing a bottleneck. This busy paper mill required ultra-pure water to protect steam generator turbines, and Envirogen stepped in to fully assess and refurbish the system to get production back on track.
Our client is one of the largest paper mill groups in Europe and at one of its busiest sites, a mixed bed ion exchange system is used to polish condensate returning from the steam generator. This water is already of a good standard, but as it passes through the generator and pipework, ionic concentration increases. To protect the ultra-pure nature of the water and recycle as much of the steam condensate as possible, a mixed bed ion exchange system is used to polish the streams and remove charged particles.
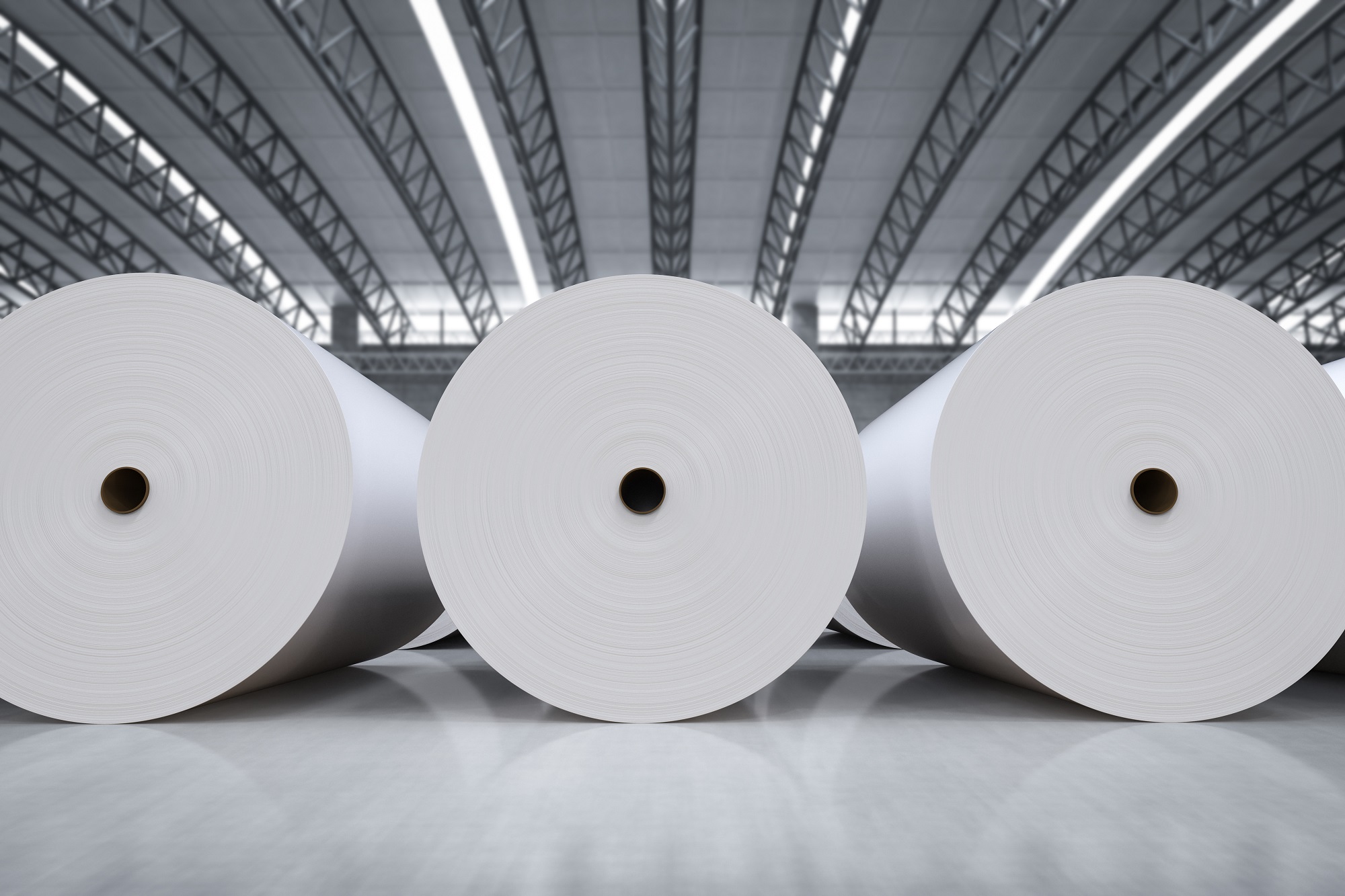
Identifying issues with a comprehensive system health check
Despite periodic servicing by the original manufacturer, the mixed bed ion exchange system needed more frequent ion exchange resin regenerations, resulting in less operating time. Each regeneration process also needed 30% longer rinsing cycles that were draining the buffer tank, causing a bottleneck in the production of ultra-pure water streams.
Although the mixed bed ion exchange plant was not an Envirogen system, we had recently completed a water treatment plant installation in one of the group’s UK paper mills and were recommended by their engineering team. We carried out a full systems health check on the entire system and ion exchange regeneration process to identify any improvements.
Bill Denyer, UK and European CEO, Envirogen, explains:
“Our health checks are a low-cost way for clients to identify issues in their water treatment or process filtration systems. Our client was seeing dramatic changes in the ion exchange regeneration process frequency, and it was clear that the system was operating at a much-reduced efficiency due to the increased amount of rinsing time and water needed. Although this wasn’t one of our installations, the process of mixed bed ion exchange systems is similar and, since our process engineers work on a variety of makes and models every day, we were able to identify issues.”
Mixed bed ion exchange water treatment systems operate by presenting a mixture of positively and negatively charged beads to water as it flows through the holding vessel. Cations, such as sodium (Na+) and magnesium (Mg++) are exchanged by cation resin and hydrogen (H+) ions are released in return. Anions, such as chloride (Cl–) and nitrate (NO3–), are similarly exchanged by the anion resin, with hydroxide (OH–). The H+ and OH– ions then recombine to form water molecules and leave the ion exchange system while the contaminant ions are captured within the resin beds.
Once the resin beds are saturated with ions, the system enters a regeneration phase. The system is backwashed from bottom to top, and the mixed bed cation and anion resin begins to separate and split into two levels: the darker, high-density cation beads move to the bottom of the vessel and the lighter, low-density anion beads to the top. Once the resins are separated, each resin is regenerated with a specific chemical: a caustic solution (NaOH), to reintroduce OH– ions to the anion beads or acid(Hcl) to regenerate the cation resins. The process lasts around four to five hours.
Once the ion exchange regeneration process is complete, the caustic and acidic regeneration chemicals are rinsed from the resin bed.
The Envirogen servicing team found that the resin bed was not separating effectively during the regeneration stage, and this was preventing the resin from being regenerated correctly. In turn, this meant the rinsing cycles took longer as the system fought to remove regeneration chemicals from the cross contamination of chemical regenerant on the reins. This caused the regen water buffer tanks being drained during this process, putting pressure on upstream supplies, and creating a bottleneck.
Solving the mix-up in the mixed bed
When the servicing team began the health check it became clear there were issues with the resins and that some anion resin had been lost from the vessel.
Denyer explains further: “We immediately saw that there was an issue with the separation level of the resins. On closer inspection inside the vessel, we could see that the anion resin level was very low. This pointed to a problem within regeneration cycles as the resin was being removed once they had split into their different levels.
“We removed the nozzles that feed the regenerating chemicals and saw they were filled with anion resin beads; with new nozzles installed to replace the faulty ones, this first issue was solved.”
To establish the capacity and effectiveness of the individual beads, samples were obtained and sent to an accredited laboratory for testing. The results showed that the beads were still of a good quality which meant that full replacement wouldn’t be needed. Added to this, incoming and outgoing water samples were measured to establish the effectiveness of the ion exchange process.
Finally, the team re-established the resin levels, refilling the lost anion resin and ensuring that the separation level was aligned for maximum regeneration effectiveness.
“The mixed bed was operating with its brakes on,” continues Denyer. “The regeneration chemicals couldn’t interact with all the resin, meaning that rinsing phase took longer, sometimes up to ten hours, as more time was needed to remove the chemicals. Because the resin was not being fully regenerated, the previous in-operation time was ineffective and reduced to days rather than weeks. Once we found the source of the problem, the recalibration was relatively simple and more efficient than replacing the entire system or the full resin bed.”
A new servicing plan protects future operations
With mixed bed ion exchange technology systems staying in operation for upwards of 20 years and resin beds typically lasting between five and eight years, it made sense for our client to protect this asset and its future operating efficiency.
The health check report contained full details on the current operation of the system and how the flushing and ion exchange regeneration processes could be made more efficient and effective in future. The engineers then gave detailed advice and training to the operators to prevent further issues from occurring.
The mixed bed ion exchange system is now protected with a PureCare maintenance plan, with full servicing support and breakdown cover. Our servicing engineers attend the site frequently and monitor the system to ensure cost-effective operation.
Key outcomes
- A full on-site health check detected the hidden problems that were causing substantial operational issues.
- A comprehensive report detailed the performance of the system and the changes needed to achieve optimum demineralisation standards.
- The client halved the amount of regeneration chemicals used per year by extending the in-operation time from one week to up to three.
- Ongoing PureCare service and maintenance plan to ensure ongoing optimisation of the system and to protect against future faults.
- Plant refurbishment and replacement of the faulty regeneration nozzle and recalibration of the split level led to:
- Reduction in rinsing time from ten hours to just five leading to a 30% reduction in wastewater streams
- Longer operational time, with regeneration now taking place once every two to three weeks rather than every week
- 50% decrease in chemicals needed to regenerate the resins, due to greater in-operation time
For a free assessment to evaluate water treatment and process filtration solutions for your site, contact our team of expert engineers
About the client
Our client is a provider of sustainable packaging solutions, paper products and recycling services worldwide