Following the decision to relocate an Oasis product line from Milton Keynes to its state-of-the-art Edmonton site, Coca-Cola Europacific Partners (CCEP) needed to re-evaluate the supply of high specification process water feeding the system. Although an interim solution was coping with the flow, it was time for a more permanent solution.
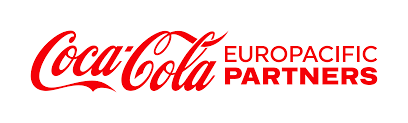
Oasis is one of Coca Cola’s more specialised soft drinks and is produced to a batch recipe that requires a specialist, high standard of process water. The site’s existing reverse osmosis system was a temporary solution, on hire and held in a refrigerated lorry outside the factory. CCEP was keen to establish a permanent solution that would meet their exacting safety, quality and environmental standards.
CCEP has a strong focus on supporting manufacturing excellence across their factories, aiming to make each process as productive, efficient and sustainable as possible. Frustrated with the standard offerings and inflexible water treatment systems offered to them from previous water treatment providers, CCEP approached Envirogen Group for a creative and fresh solution.
Keeping it clean with hygienic stainless steel
Envirogen designed a stainless-steel construction consisting of a reverse osmosis skid, along with an antiscalant dosing system, permeate pumps, 15,000-litre permeate storage tank, ultraviolet (UV) sterilisation skid, polished components and hygienic connections.
“It was clear from the outset that CCEP needed a very high standard of process water,” explains Bill Denyer, UK and European CEO, Envirogen. “The water needs to be stored in tanks, ready to feed the process line when required. It is continually recirculated around the UV and ring main system to maintain purified water standards and to ensure the perfect product quality that Coca-Cola demands.”
“We design process filtration and water treatment systems for many different manufacturing processes in the food and beverage market and our team is experienced in working with this level of hygienic, stainless-steel design.”
“We engineered every pipe, connection and bend to inhibit and control bacterial growth and we manufactured completely smooth bores and provided tri-clover connections rather than flanges, to prevent crevice formation within the pipework.”
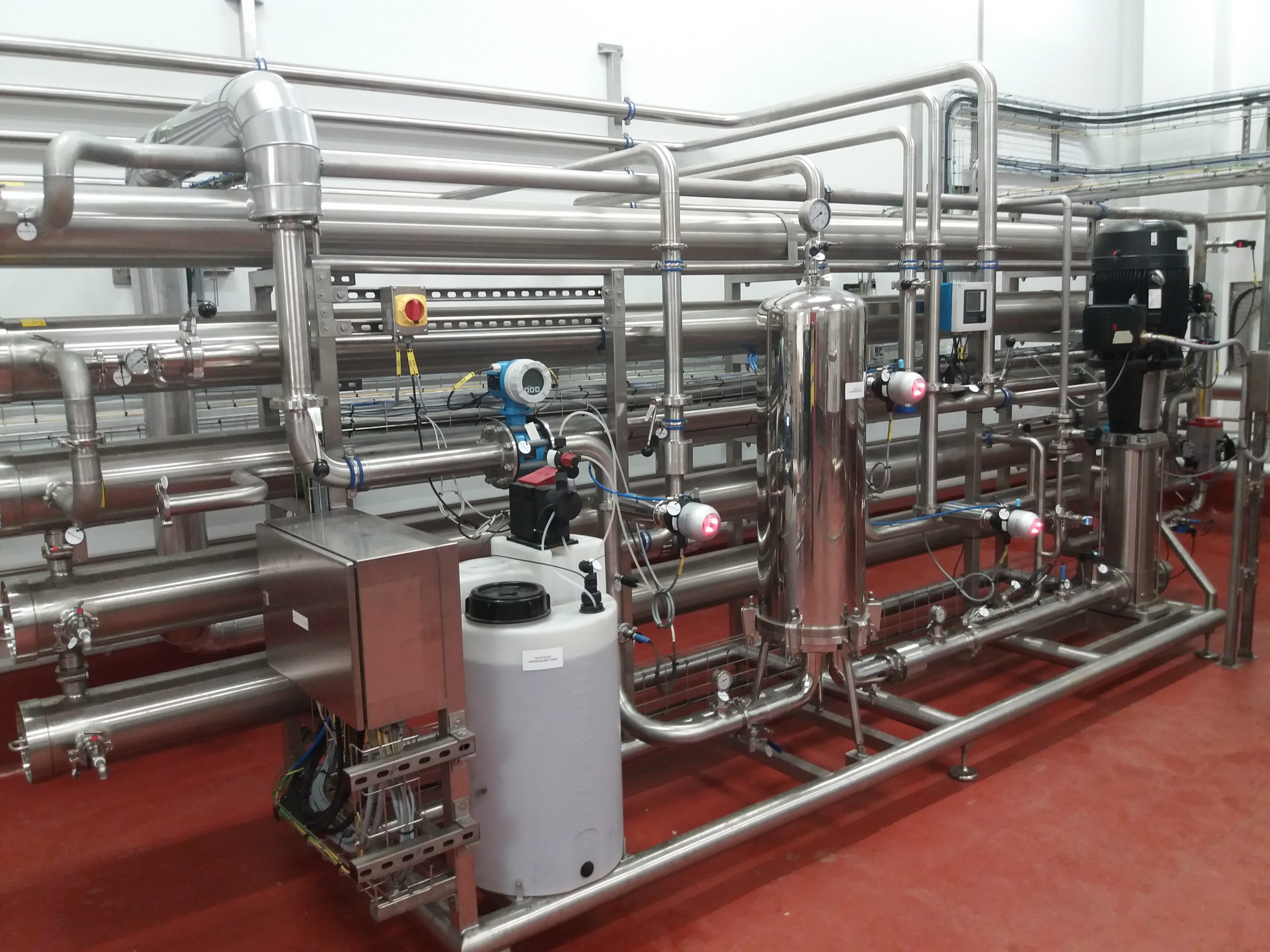
Envirogen Group’s PureSep RO plant: hygienic reverse osmosis system
Sustainable water solutions at the KORE
The whole system was built to Coca Cola’s own KORE standards. These standards are some of the most exacting in the food and beverage sector and reach across all product safety and quality, worker health and safety and environmental areas. The system was built to comply with each and every standard, from engineering specifications and electricity regulations right down to the tags attached to each pipe.
A key part of KORE is sustainability; for this reason, CCEP was keen that all wastewater streams be reduced.
“All beverage products have a high percentage of water content,” continues Denyer. “You want the vast majority of the incoming water to be used for the end product and you want to ensure that as small a percentage as possible is wasted. A standard reverse osmosis system typically has a water recovery rate of around 75%. By engineering an additional nanofiltration module to run in series with the reverse osmosis array, we were able to raise that recovery up to 90%.”
“The first stream of filtered water was sent directly to the permeate storage tank and then the 25% in the waste stream was sent to the nanofiltration module to be processed again. The recovered water is sent back to the reverse osmosis inlet and the waste is sent to effluent storage tanks to be treated alongside the other waste streams from the site.”
“We needed to ensure that the dissolved ions and other impurities are kept in solution, whilst maximising the amount of purified water that we can feed into the process. The concentrated waste stream can easily be disposed of with the wastewater volume kept as low as possible.”
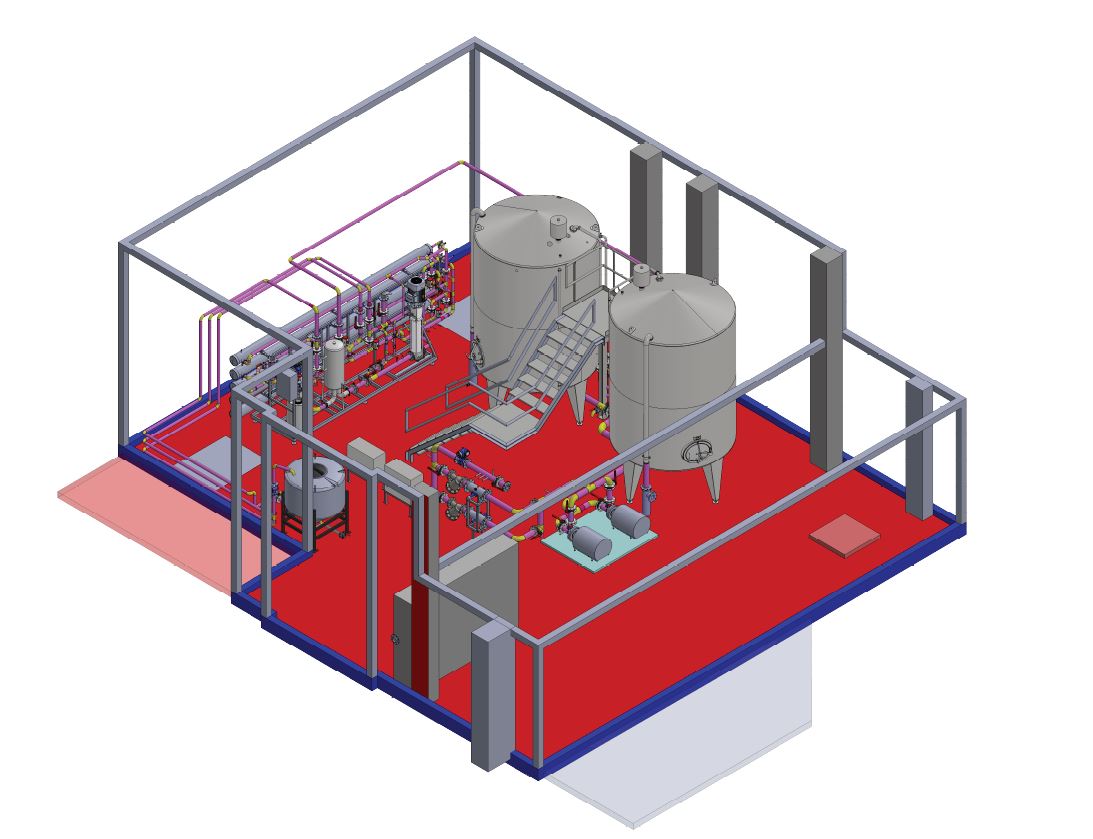
Ensuring ongoing success for the Edmonton site
The system was built and commissioned to the specific timeframes and project milestones set by the client. As the system was built alongside the existing mobile skid, switchover could happen instantaneously with no impact on manufacturing, either to the Oasis or other Coca-Cola manufacturing lines.
Envirogen’s involvement didn’t stop when the system was put live. CCEP signed up to a tailored service and maintenance package to ensure ongoing optimisation of the system. With a prompt, local service, dedicated engineers maintain the CCEP Edmonton plant.
Timely and secure supply of consumable cartridges is also supplied for the reverse osmosis and UV sterilisation system, with stock held locally to meet demand.
Following this project, CCEP commissioned the Envirogen team to begin work on an entire process water treatment plant for the separate Wakefield site.
Read more about the CCEP Wakefield process water treatment plant case study.
Key outcomes
• System engineered to ensure a very high standard of process water suitable for a batch process.
• Hygienic and entirely stainless-steel PureSep RO reverse osmosis and UV sterilisation system designed to meet Coca-Cola’s KORE standards.
• Water recovery rates of up to 90% achieved.
• Ongoing service, maintenance and consumables plan ensures ongoing optimisation and efficiency of the water processing system.
• CCEP’s manufacturing excellence ambitions are supported to help the site become as productive, efficient and sustainable as possible.
For a free assessment to evaluate water treatment and process filtration solutions for your site, contact our team of expert engineers
About the client
CCEP is the largest Coca-Cola bottler by revenue, with over 23,000 employees working in 13 Western-European markets. CCEP makes, sells and distributes some of the world’s best-loved drinks to millions of customers and consumers.
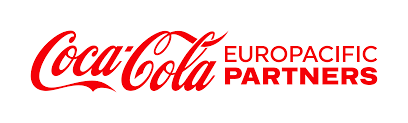