Envirogen is an industry leader in the use of bioreactor technology, with over 40 FBR systems installed worldwide and several projects under development. The Envirogen fluidized bed reactor is a proprietary biological water treatment system deployed to remove organics or oxyanions (i.e., nitrate, selenium, perchlorate) from water. It can achieve high treatment efficiencies of greater than 99% as an active, fixed-film bioreactor that fosters the growth of microorganisms on a hydraulically fluidized bed of specified media (e.g., granular activated carbon (GAC) or sand). Because the media particles are small and suspended, they present a large surface area for microbial growth and attachment.
The fluidized bed allows for high concentrations of attached biomass and consistent performance under steady-state conditions without backwashing. As the microorganisms acclimate and grow, the number of attached microbes per media particle increases creating an expanding “living” media bed. As the “living” media bed expands and fluidizes further, the bed reaches a control point where a patented device (i.e., biomass separator) gently shears excess biofilm from the media surface. The sheared suspended biological solids are continually discharged with the treated water and if required, can be removed after the fluidized bed reactor by typical filtration systems.
For a FREE, no-obligation assessment on how you can save energy, water, waste and money, contact our team of expert engineers
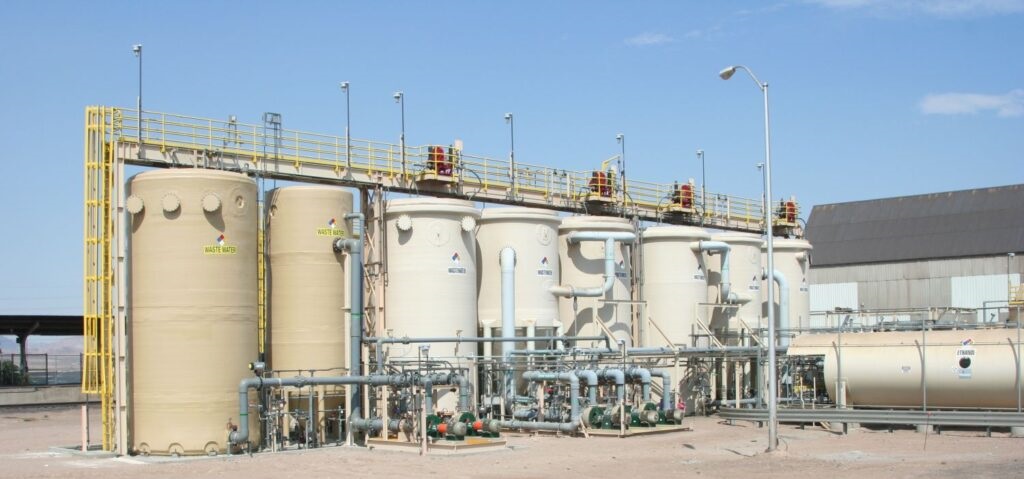
Types of FBRs Available
The FBR can be provided in an aerobic, anoxic, or anaerobic configuration:
-
- Aerobic systems: The FBR system is supplied with air or oxygen to promote aerobic metabolism, where the organic contaminants entering the system serve as a growth and energy providing substrate.
- Anoxic systems: A growth substrate (e.g., acetic acid. ethanol, methanol, etc.) and a phosphorus nutrient are supplied to the fluidized bed bioreactor, which promotes metabolism by the attached microorganisms of all the dissolved oxygen, nitrate, nitrite, perchlorate, selenium and other metals.
- Anaerobic systems: More recalcitrant organic contaminants are supplied as a growth and energy substrate without the presence of oxygen. Metabolism of these organics occurs and methane gas is formed. This gas can be flared or captured for beneficial reuse.
How does a fluidized bed reactor work? An overview of Envirogen’s patented FBR treatment process/fluidized bed reactor design. (US Patents: 6706521, 5750028, 5788842, 7754159, 7611890, 7572626, 8323496, 6830922).
Markets and Applications
Suitable for a broad range of influent flow rates and contaminant concentration levels, Envirogen’s FBR containerized/mobile designs provide low-cost installation. Our treatment systems have been successfully operated at ranges from 50 to 6,000 gpm while simultaneously providing high performance at low capital and operating costs.
Markets:
- Mining
- Power
- Remediation
- Municipal
- Refining
Applications:
- Organics like chlorinated solvents, BTEX, MTBE/TBA, and 1,4-Dioxane, and NDMA
- Oxyanions such as nitrate, perchlorate, chlorate, and selenate
- Emerging contaminants like 1,4-Dioxane, NDMA, 1,2,3-TCP, and hexavalent chromium
A flexible and adaptable approach to technology means we can provide additional add-on modules to tackle a range of downstream applications including suspended solids separation and handling.
System Advantages
- Small footprint and highly efficient: High concentration of biomass, plug-flow characteristics and tall vessels and media beds minimize bioreactor footprint. High biomass concentration means long solids retention time (SRT), short hydraulic retention time (HRT) and a high-quality effluent.
- Steady-state performance: FBRs run continuously without backwashing or cleaning operations.
- Robust: Does not plug up or channel. Tolerant of high-feed total suspended solids (TSS) and metals. Proven robust performance and ability to quickly recover from upsets such as power outages or loss of chemical feeds. Capable of handling both hydraulic and contaminant shock loads.
- Flexible: Operates effectively over a wide range of feed flow and qualities. An actual treatment technology (“green”) and not just a phase transfer treatment for most contaminants.
- Proven design: Envirogen’s fluidized bed reactors have been continually improved and refined based on lessons learned over 30+ years of design and operating experiences.
- Cost-effective: Envirogen’s FBRs are cost effective across a wide range of contaminants and flowrates treated.
Fluidized Bed Reactor Frequently Asked Questions
How does a fluidized bed reactor work?
Used to treat contaminated water, the fluidized bed reactor uses a fluidization pump to hydraulically suspend or fluidize the media bed vertically. This media supports the growth of specially selected microbes that act to degrade or consume toxic contaminants such as nitrate, selenium, perchlorate, 1,4 dioxane, and others.
What is a fluidized bed used for?
Although commonly used to facilitate chemical reactions, fluidized beds are also used as an active water treatment system to remove recalcitrant contaminants. The Envirogen fluidized bed reactor uses specialty microbes, grown on a fluidized media, to transform toxic contaminants so that the effluent can be safely discharged.
What is the difference between fixed bed and fluidized bed?
In a biological fixed bed system, the media bed is packed into a vessel and is not moving. In a fluidized bed, water flows at a set flow rate to cause the media bed to hydraulically rise, where it remains in this fluidized state during treatment. By fluidizing the media, all the media surface area is exposed and available for the task of removing harmful contaminants.
What are the advantages and disadvantages of a fluidized bed reactor?
Fluidized beds used in water treatment applications tend to have smaller footprint/overall system size then fixed bed counterparts. In addition the system can run continuously without backwashing. If forward feed needs to be stopped, the microbes remain fluidized in the reactor and can be maintained in a “ready state” to initiate treatment once feedwater is restarted. A potential disadvantage of fluidized bed reactor technology is that additional electrical costs might be incurred to operate the system continuously in a fluidized state. However, this cost is often offset by the numerous advantages previously conveyed.
Envirogen Life Cycle Cost Assurance Programs
For ongoing peace of mind, our fluidized bed reactor systems are backed by a performance guarantee over the lifetime of the installation, creating the best opportunity for an optimized life-cycle cost. This manages the risk of non-compliance and allows clients to focus on their core business.
Envirogen has over 20 years of turnkey design, installation, and operations and maintenance (O&M) experience with dewatering and groundwater turn-key remediation projects at more than 100 sites. Our integrated O&M offering includes engineering, process, treatability, and other technical services as important components. This commitment of technical expertise in support of O&M allows us to be flexible to adapt to changing conditions for maximum reliability.
Speak to our team of experts to discover how biological fluidized bed reactor technology could help you in removing organics, oxyanions, and emerging contaminants from water